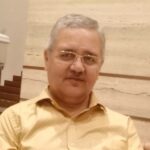
Corrosion can weaken buildings and structures, gradually damaging them and leading to costly repairs over time. To mitigate this, the need of this hour is to appropriately analyze the causes of corrosion and come out with the appropriate solution. Addressing these, requires experts who can blend knowledge from concrete, material science, civil engineering, and advanced testing methods.
In regard to this, Constrofacilitator.com recently had a conversation with Er. C K Baxi, a distinguished specialist in Concrete Technology & Forensic Engineering. He currently serves as the Technical Director at Prudent Forensic Consultancy Private Limited and holds the position of General Manager at K K Retroflex Solutions. He is a highly skilled specialist with a profound comprehension of materials, corrosion mechanisms, and failure analysis. In his role as a consultant for Corrosion and Forensic Engineering, he excels in offering diagnostics, mitigation strategies, and rehabilitation solutions.
During the interview, he shared insights encompassing the overview of corrosion and forensic engineering, assessment methods, approach techniques, and emerging technologies.
Here are the excerpts from the inerview.
Can you provide an overview of your experience in corrosion and forensic engineering, as well as the types of projects you’ve worked on? What types of corrosion can structures experience?
I’ve handled assignments involving corrosion in both concrete and steel structures. It might seem unconventional, but concrete can indeed undergo corrosion, primarily through the depolarization of cement. This results in heterogeneity and loss of integrity within the concrete matrix. Such corrosion is common in structures exposed to corrosive chemicals and conditions.
Concrete corrosion presents signals that must be timely detected for detailed investigation, preferably through non-destructive testing. An extensive analysis and evaluation of test results help establish links between different conditions causing damage, leading to the identification of root causes. This is essential for designing structural rehabilitation plans to prevent recurrence of damage.
Concrete corrosion indicators include:
- Spalling
- Surface cracks with significant depth/width
- Exposed reinforcement bars
- Honeycomb effects on the surface
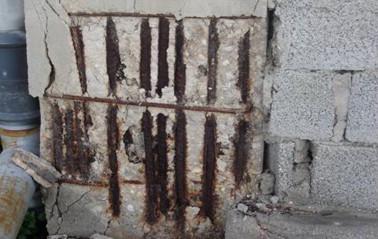
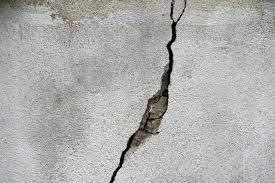
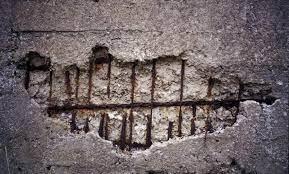
Various concrete concrete corrosion indications- spalling, surface cracks and exposed reinforced bards
Identifying steel corrosion is comparatively easier, as the visible rust product on the surface indicates its presence. Types of steel corrosion include mild, medium, severe, and spot/dot corrosion. Corroded steel structures should undergo relevant tests to determine the extent and seriousness of corrosion-induced damage. Reverse engineering is crucial for designing structural rehabilitation plans for such cases.
As a Corrosion Engineering expert, how do you assess potential corrosion risks in critical structures, both steel and concrete?
The potential risks in critical or non-critical structures due to corrosion involve the loss of integrity in concrete or steel members. Depolarization of the matrix leads to loss of homogeneity, causing aggregates in concrete and web/flange in steel members to function independently, an unhealthy situation.
Understanding corrosion chemistry for both concrete and steel structures is sometimes essential. The corrosion process, causal conditions, and atmospheric factors need careful examination, as they vary with each assignment.
In forensic engineering, how do you differentiate between corrosion-related failures and failures caused by other factors like material defects?
Distinguishing between corrosion-related failures and other causes is a crucial step in designing corrosion mitigation strategies. Forensic Engineering relies on test results, much like how medical tests aid pathologists in diagnosing illnesses. Damaged concrete or steel members must undergo relevant tests, predominantly non-destructive ones, although a few might involve particle puncturing.
A correlation between the test results and standard parameters, tested during the examination, is crucial. Visual inspection and observations help correlate deviations in test results. For instance, a “good” rebound hammer test result for concrete doesn’t necessarily mean good compressive strength; it might be due to carbonation effects if the depth of carbonation equals or exceeds the cover depth.
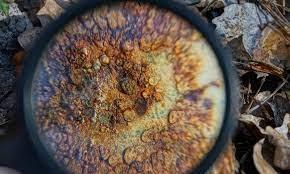
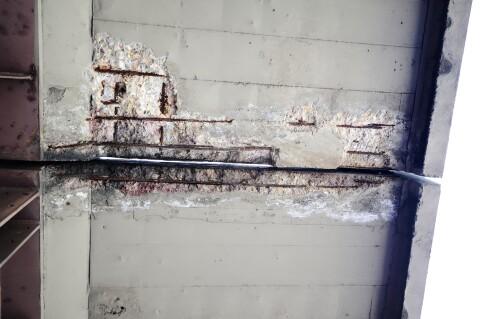
Corrosion-related failure and failure due to material defect
In your experience, what are common misconceptions about corrosion’s effects on steel and concrete structures?
Common misunderstandings exist in both steel and concrete corrosion. Common misconceptions are briefly addressed below:
Steel Corrosion:
- Severity of corrosion varies with steel surface exposure to corrosive conditions. Dot or spot corrosion isn’t always serious.
- Sustained corrosion leads to member thickness reduction, impacting load-sharing capacity. Regular examination of corroded steel surfaces is crucial.
- Corrosion accelerates faster in corners and angles compared to plain surfaces.
Concrete Corrosion:
- Concrete corrosion occurs due to depolarization of the matrix, causing a loss of cement’s binding properties.
- Unlike visible rust in steel corrosion, concrete corrosion doesn’t offer clear visual signals.
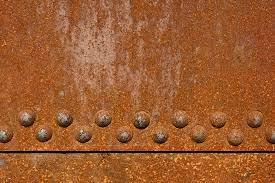
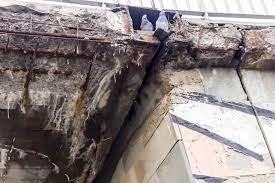
Steel corrosion and concrete corrosion
What emerging technologies or methodologies in corrosion and forensic engineering do you find promising?
Forensic Engineering begins with precise testing to identify parameters that trigger the need for investigation. Various testing methods for concrete and steel regularly undergo upgrades due to evolving damage patterns. Emerging tests include thermography for concrete and drone surveys and tomography for corroded concrete and steel members.
How do you effectively communicate your findings and recommendations to clients, stakeholders, or non-technical individuals?
After testing, systematic record-keeping is vital, following internationally accepted standards. Forensic Engineering-based presentation of results requires comprehensive interpretation, evaluation, and analysis. Report preparation is an art mastered to convey case facts in a simple and understandable manner to clients.
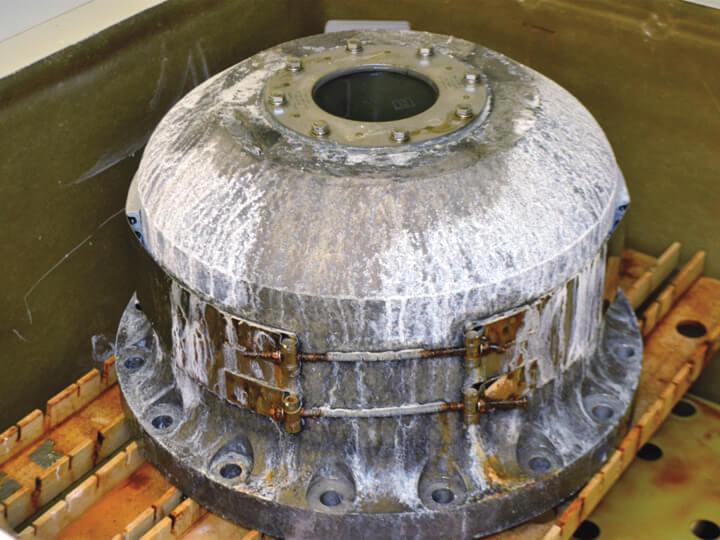
Corrosion Testing
What advice would you offer to aspiring engineers interested in specializing in corrosion and forensic engineering?
I would impart three principles: cultivate a genuine passion for your work, maintain a deep commitment to your assignments, and view failures as stepping stones for improvement. It’s vital for engineers to have a firm grasp of foundational concepts to effectively analyze challenging conditions. Test results are only figures; true insight is gained when those figures are grounded in a solid understanding of fundamentals. This forms the bedrock of forensic engineering analysis.